Rokko Butter Co., Ltd.
We make the most of cheese by approaching people to continue to eat it as well as making good quality cheese.
Rokko Butter was founded in 1948 as Heiwa Oil & Fat Industry Co., Ltd., which manufactured margarine designated by the Ministry of Agriculture and Forestry.
In 1954, we renamed our company name to Rokko Butter Co., Ltd. and began to produce processed cheeses using natural cheeses imported from Australia in 1958, releasing the Q・B・B brand nationwide.
In 1968, we started a mass production system at the existing Inami Factory. In 1971, we developed and released the first individually packaged sliced cheese in Japan.
Based on the Q・B・B brand, we create good-quality cheeses as the top brand of processed cheeses, and also we make good use of cheeses in the human body through customers continuing to eat them.
We believe that this is the responsibility that Q・B・B should fulfill, and we are creating new value for processed cheeses and creating products that meet our customers' needs.
INDEX
The new factory construction project
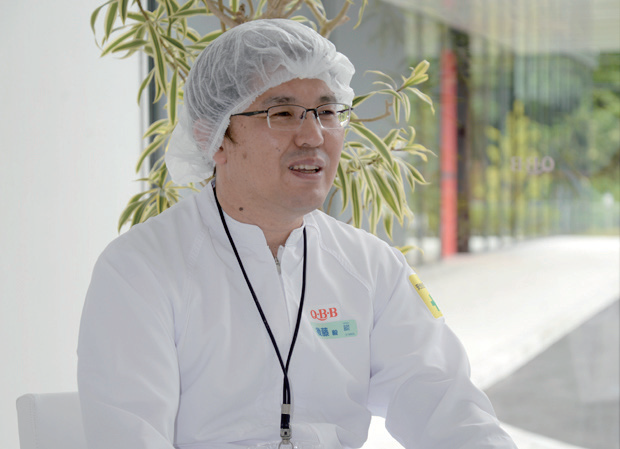
Demand for cheese is high in domestic and overseas (particularly in Southeast Asia and so on). And the market for processed cheese is growing due to the rising demand for drinking at home in addition to the westernization of food and increased health consciousness.
Meanwhile, the current Inami Factory, our main factory, has been in operation for 50 years.
It is difficult continuously to meet the quality requirements from customers for safety and security. And buildings were scattered across a limited production space. For these reasons, we have started a project to build a new central plant that replaces the aging Inami Factory to increase production capacity and consolidate/streamline each process.
The operation status of the new factory (hereafter Kobe Factory) construction project
- Optimal layout of production lines and introduction of the latest production equipment
- Centralized management of information and a high-level quality management system
- Automation of in-plant logistics
- First introduction at Rokko Butter of Manufacturing Execution System!
- Uses AI and IoT for high productivity and excellent energy efficiency!
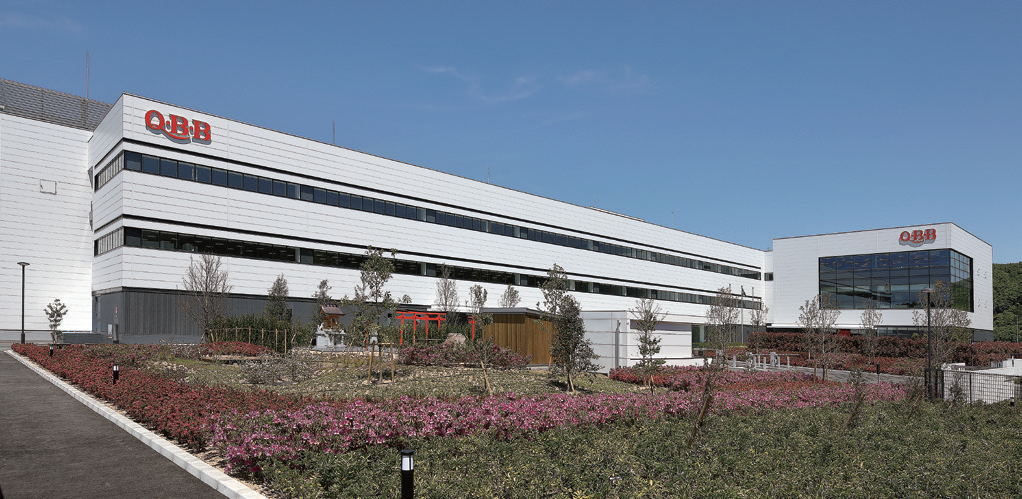
Introduction effect
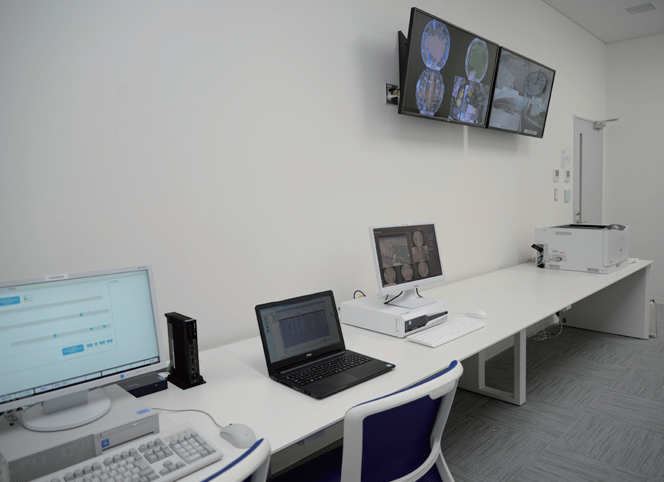
Equipment and robots for automation are only partially optimal if they are introduced on a stand-alone basis.
The "Manufacturing Execution System" (hereafter "MES") is the core system to support automation by sending instructions and receiving results as information linkage to automation facilities.
First, the raw materials and production materials that arrive at the factory are transferred to a factory pallet. And on entering the automatic warehouse, they are linked with the pallet number, and the warehousing instruction is linked to the warehouse management/transport management system (WMS).
At the time of production, production instructions are received from the core system, the required amount of raw materials and production materials is calculated, and batch processing is deployed.
To carry out the automatic transfer to the site, the instructions (when, what, and how much to use from inventory) are linked to the WMS.
The actual supply timing is automatically supplied just-in-time by coordination between facilities.
After packing products in boxes, they are automatically palletized. Here again, the scheduled data is sent from the MES to the production facility (PLC), and palletizing results are automatically collected and linked to the sales management system.
Through this type of data linkage, automation is realized by "connecting" facilities to facilities and systems to systems.
These data at sites are also very important for factory management.
MES manages inventory in real time and works closely with the core system, and is also utilized in the Amoeba management promoted by Rokko Butter.
We have established traceability by managing the results of a series of products, people, and facilities.
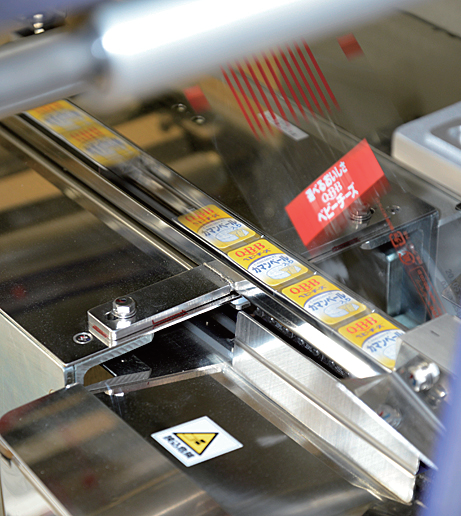
Future prospects
Introducing MES, automated transport, and automated warehouses is the first experience for Rokko Butter.
It was necessary to satisfy the requirements from a variety of perspectives, such as user-friendliness considering the operation, facilities, and flow lines, error prevention, and establishment of traceability.
We were able to realize this systemization by having Shimizu Corporation and YOKOGAWA take the lead in considering a system that "connects" the WMS/core system with the data.
In the future, we will concentrate manufacturing technology on the Kobe Factory, which will be our main factory replacing the Inami Factory, and continue to provide safe and secure products in addition to establishing a system to further increase production.
Also, we plan to acquire bonded factory certification as a production base for products for exports to the expanding markets of Asian peripheral countries, Europe, and the United States. And we will create a foundation to transmit our product information to the world as "the Best Processed Cheese Plant in the Asia.
Among them, MES's role has become increasingly important. We also have high hopes for YOKOGAWA's support, and we want both systems and people to grow and develop.
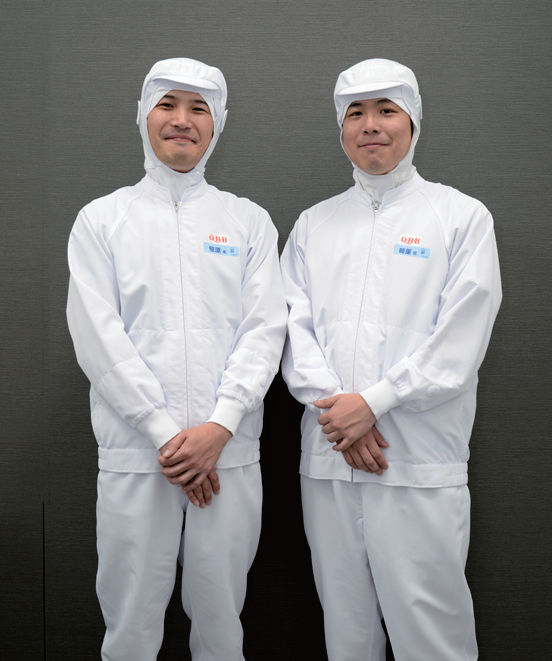
Company overview
Company name | Rokko Butter Co., Ltd. |
---|---|
Head office | 1-3-13, Sakaguchidori, Chuo-ku, Kobe |
Founded | December 13, 1948 |
Business description | Production and sales of foods mainly containing cheeses and milk etc. |
URL | https://www.qbb.co.jp/english/ |
Industries
-
Food & Beverage
At Yokogawa, we understand that today’s food and beverage companies face unprecedented challenges in climate change, consumer demand, and increased global competitiveness. Overcoming these challenges will require innovative solutions that focus on key areas of production, asset management, and food safety and quality.